This paper analyzes the above situation in - depth and summarizes technical measures to solve the problems.
1. Main Problems of SPD Products in Voltage Transformer Secondary Circuits
Currently, there are residual - current - free SPDs (switch - type lightning arresters) at home and abroad. Their main internal discharge circuits use discharge tubes/gaps, with high discharge current capacity (exceeding zinc oxide varistors). However, they have fatal flaws: poor voltage - limiting, arc - pulling voltage, and long response time (up to 100 ns). These prevent the secondary circuit equipment from getting proper protection. Worse, arc - pulling voltage often drops the voltage transformer's secondary circuit voltage (100 V) to several volts, making the measurement and control system show high - voltage line voltage loss. Thus, switch - type lightning arresters are unusable.
2. Solutions and Main Contents
Common SPD core discharge elements in the market include discharge tube CDT, zinc oxide varistor MOV, and transient voltage suppressor TVD. TVD has ultra - fast response (1 ns), good voltage - limiting, and small residual current (below 1 μA); it burns out and disconnects after damage, without short - circuit. But its discharge current is low (1 kA). Also, CDT, GAP, and TVD have stronger high - voltage anti - impulse capability than MOV, withstanding 10 kV impulses without structural damage.
By combining these elements' advantages and using a combined circuit, a product (MOV in series with parallel CDT and TVD) is designed, as shown in Figure 1.
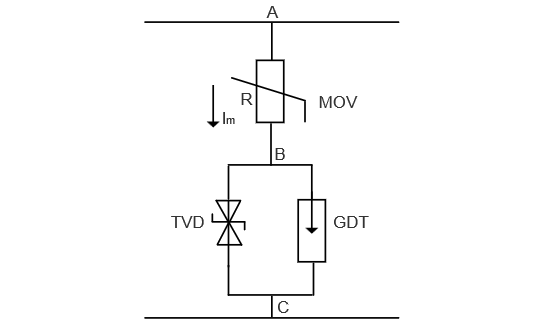
Figure 1: Discharge Principle
When lightning current intrudes at Point A, the MOV remains non-conductive initially. However, the residual current of MOV equalizes the potential between Points A and B. At this moment, the TVS activates within 1 ns, creating a direct path between Points B and C. Consequently, the full lightning voltage is applied across the MOV between Points A and B. Since the MOV's activation voltage Um is only 50% of the combined circuit's activation voltage Uc, the high voltage accelerates the MOV's activation, reducing its typical 25 ns response time to approximately 12.5 ns. During this period, while the discharge current is still building, the direct path from A to B forces most of the lightning voltage across Points B and C (where the TVD’s maximum current capacity is ~1 kA).
From a design perspective, the CDT’s activation voltage is 50% lower than Uc. Additionally, the internal resistance RL of the partially conductive MOV creates a voltage drop that elevates the voltage at Point B above the initial lightning voltage. Testing shows this reduces the CDT’s activation time from 100 ns to 15 ns, enabling the entire circuit to fully conduct within 25 ns—matching the response time of a standalone MOV.
After discharge, the TVD’s negligible residual current and the CDT’s complete disconnection eliminate MOV residual current issues, preventing potential hazards. For voltage clamping performance, the TVD’s precise activation (where activation voltage equals clamping voltage) ensures a low clamping threshold. Given Um = 0.5Uc, MOV’s clamping voltage within the circuit is 1.5Uc, resulting in an overall combined circuit clamping voltage of 2Uc—significantly better than the 3× ratio of standalone MOV modules.
An additional monitoring circuit is integrated to detect component failures. When internal elements degrade, the monitoring node transitions from open to closed, signaling SPD failure. Table 1 compares the performance of standalone MOV modules versus the combined discharge circuit SPD under identical conditions.
This new - type SPD has residual current, yet it can control the over - voltage at a very low level (below 10 μA). Moreover, it can keep the residual current parameters unchanged, and quickly disconnect after the over - voltage disappears. It is an ideal product applicable to the secondary circuit of voltage transformers.
The SPD adopts a combined discharge circuit to replace the single zinc oxide varistor module, providing over - voltage protection technical measures for the secondary circuit of the voltage transformer. It can avoid the problem of increased aged residual current after the SPD circuit is impacted by lightning or operating over - voltage multiple times. Meanwhile, when breakdown and failure occur, there will be no short - circuit phenomenon. If the SPD has fault sites such as breakdown and short - circuit, the operation and maintenance personnel can be reminded through the alarm contact point of the SPD, avoiding the occurrence of protection mal - operation or non - operation problems.
3. Conclusion
In the actual use process, the SPD adopting the combined circuit has the residual current value basically unchanged from the start to failure (after damage, it is directly disconnected), and can be controlled below less than 3 μA. Moreover, the SPD can conveniently provide a failure monitoring contact point through the combined circuit, which is easy for operation and maintenance personnel to monitor.
By adopting the over - voltage suppression technology for the secondary circuit of the combined voltage transformer, the risk of protection safety mal - operation or non - operation caused by the grounding hidden danger of the SPD in the secondary circuit of the voltage transformer is avoided. It truly realizes the protection against lightning and operating over - voltage in the secondary circuit of the voltage transformer, ensuring the safe operation of the power secondary equipment in severe weather environments and accident situations.