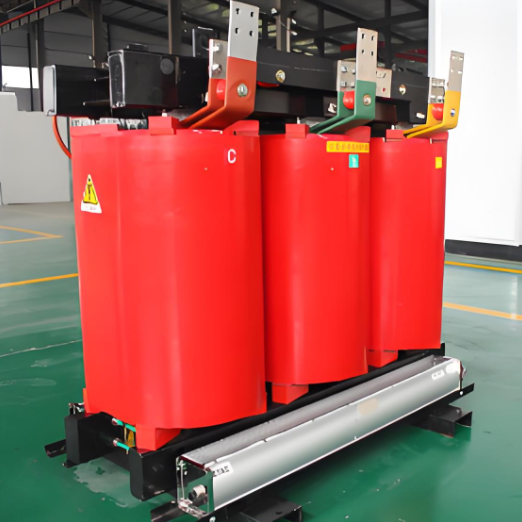
Dry-Type Transformer Solution: Dedicated System for Demanding Industrial Environments (Anti-Corrosion / High Overload Dry-Type System)
1. Challenges Addressed
- Industries: Chemical, Metallurgy, Shipbuilding, Coastal Energy Facilities, etc.
- Environmental Threats:
- Extreme High Humidity: Constant or long-term ambient relative humidity > 90%.
- Corrosive Attack: Presence of highly corrosive media including salt spray, acidic/alkaline gases (pH range 2-12), chemical vapors.
- Operational Stress: Production processes may require transformers to withstand significantly exceeding their rated load capacity for short durations.
- Physical Shock: Need to withstand plant vibration and seismic risks (e.g., in coastal/industrial zones).
2. Core Solution Overview
Designed specifically to withstand the extreme industrial environments above, this solution integrates cutting-edge material technology and structural reinforcement, providing triple-core protection: Exceptional anti-corrosion sealing, Robust dynamic overload capability, and Rugged mechanical shock/earthquake resistance. This ensures long-term, safe, and reliable transformer operation under adverse conditions.
3. Core Technology & Configuration Details
- Specialized Protection - Building an Anti-Corrosion Barrier:
- Winding Protection (Core Defense):
- Utilizes vacuum casting/impregnation process with nano-SiO₂ particle modified epoxy resin.
- Advantage: Nano-SiO₂ significantly enhances the resin's density and hydrophobicity, forming an ultra-strong physical and chemical barrier that effectively blocks moisture and corrosive media penetration.
- Performance Certification: Winding salt spray corrosion resistance rating reaches ISO 12944-C5M (Marine/Very High Industrial Corrosion level).
- Enclosure Protection (External Fortress):
- Option 1 (Highest Protection): 316L Stainless Steel Enclosure. Offers excellent resistance to acids, alkalis, and chloride corrosion.
- Option 2 (Cost-Effective): High-Quality Carbon Steel Enclosure + High-Performance Fluorocarbon Spray Coating (FEVE or PVDF).
- Protection Capability: The enclosure protection system withstands acidic/alkaline chemical attacks within pH 2 to 12, perfectly suited for demanding scenarios like chemical plants and acid cleaning workshops.
- Dynamic Overload Capability - Ensuring Production Resilience:
- Employs Class H (180°C) insulation system, substantially increasing thermal performance margin.
- Key Performance: Allows the transformer to operate safely and continuously under 120% rated load for at least 2 hours.
- Temperature Rise Control: Advanced cooling design and temperature control systems ensure the hottest spot temperature rise of the windings is strictly controlled to < 115K during such overload periods, preventing accelerated insulation aging.
- Structural Reinforcement - Withstanding Physical Shock:
- Overall structure features seismic reinforcement design.
- Certification Standard: Certified according to IEC 60076-11 standard.
- Seismic Capability: Withstands horizontal ground acceleration up to 0.3g, ensuring structural integrity and functional safety in seismically active zones or industrial environments with strong vibrations.
4. Solution Benefits Summary
- Extreme Corrosion Resistance: Nano-enhanced winding protection + high-performance enclosure enables ultra-long service life in salt spray, high humidity, and chemically corrosive environments.
- Resilient Power Supply: Class H insulation coupled with precise temperature control gives the transformer strong temporary overload capacity, adapting to fluctuating industrial production demands.
- Robust & Durable: Professional seismic design ensures stable operation under vibration and earthquake threats, reducing unplanned downtime risk.
- Safe & Reliable: Multi-layer protection design effectively isolates environmental threats, significantly reducing insulation failure risk, and safeguarding personnel and equipment.
- Reduced Maintenance Cost: Exceptional protection characteristics greatly reduce environment-driven maintenance needs, lowering total lifecycle cost.
5. Validation Case - Successful Implementation at a Coastal Refinery
- Scenario: A large coastal refinery project with long-term ambient humidity up to 95% and strong salt spray corrosion.
- Application: Dry-type transformer designed according to this solution.
- Operational Performance: Over 10 years of continuous operation, the transformer winding insulation resistance remained consistently stable at levels exceeding 5000 MΩ.
- Conclusion: This case empirically demonstrates the solution's superior protective efficacy and long-term insulation reliability in extreme high-humidity, high-corrosion industrial environments.