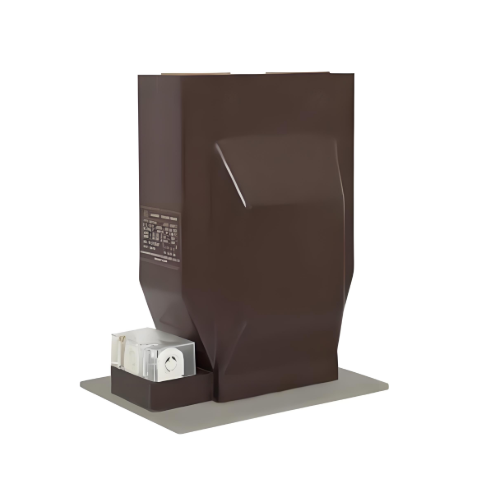
Application Background
Substations in coastal areas, chemical industrial parks, and regions with high salt-fog experience extreme environments characterized by persistently high air humidity (RH > 85%) and high concentrations of salt and industrial pollutants. Such environments pose significant challenges to current transformers (CTs) within AIS switchgear:
- Insulation Deterioration: Moisture and pollutants (salt, dust, chemical aerosols) adhering to and dissolving on insulation surfaces form conductive layers, significantly reducing surface resistance and inducing surface flashover (pollution flashover).
- Internal Condensation: During temperature fluctuations, the humidity inside the compartment can easily reach saturation, forming water droplets that directly threaten the long-term reliability of internal electrical connections and insulating materials.
- Corrosion of Metal Components: Corrosive agents like chloride ions and sulfur dioxide accelerate rusting of metal enclosures and connectors, leading to reduced structural integrity, degraded electrical conductivity, and even fracture risk.
Conventional AIS CTs exhibit significantly higher failure rates in such environments, shortening equipment lifespan and jeopardizing the secure and stable operation of the power grid. This solution specifically targets these issues with reliability enhancement measures.
Core Solutions
1. Hydrophobic Composite Insulation Technology
- Core Technology: Coating the surfaces of CT external insulators and critical insulation components with Fluorinated Ethylene Propylene (FEP) material.
- Key Characteristics:
- Exceptional Hydrophobicity: Static contact angle **>110°**. Water forms distinct droplets on the surface, preventing spread and effectively resisting wetting and penetration.
- Persistent Anti-Pollution: Even under severe pollution (e.g., simulated salt-fog environment), the coating maintains excellent hydrophobic migration properties, preventing pollutants from forming a continuous conductive water film.
- High Volume/Surface Resistance: After a rigorous 480-hour salt spray test (ASTM B117 or equivalent), surface resistivity remains above 10¹² Ω, far exceeding conventional epoxy resin or porcelain insulation materials, drastically improving pollution flashover resistance.
- Benefit: Significantly reduces pollution flashover risk, ensuring long-term insulation stability in high-humidity, high-pollution environments.
2. Active Anti-Condensation Control System
- Core Technology: Integrating a PTC (Positive Temperature Coefficient) self-regulating heating element within the CT compartment/chamber, linked with a high-precision humidity sensor to form a closed-loop control system.
- Operating Mode:
- Humidity sensors monitor compartment relative humidity (RH) in real-time.
- When detected RH > 85% (configurable threshold), the control system automatically activates the PTC heating element.
- The heating element operates (rated power ~15W), gently raising the internal air temperature.
- Control Target: Maintain compartment temperature always > Dew Point Temperature + 5°C.
- Key Protection: Precise temperature control ensures the internal relative humidity remains well below saturation (e.g., the 85% RH threshold), completely preventing water droplet formation.
- Benefit: Eliminates risks associated with condensation, including internal insulation moisture absorption, corrosion of metal parts, and electrical short circuits.
3. Anti-Corrosion Structural Design
- Material Upgrades:
- Main Enclosure: Utilizes 316L Stainless Steel, offering far superior resistance to pitting and crevice corrosion in chloride-containing environments (e.g., salt-fog, chemical atmospheres) compared to conventional 304 stainless or carbon steel.
- Surface Enhancement: Applies an AlMg₃ (Aluminum-Magnesium Alloy) sacrificial anode coating to critical connection points or vulnerable areas. This coating provides active cathodic protection, further enhancing overall corrosion resistance.
- Reliability Validation: The complete structural design must pass stringent testing according to ISO 9227 Salt Spray Test Standard Class C5-H (highly corrosive industrial and marine environments), typically requiring thousands of hours of testing. This represents the highest international corrosion environment rating.
- Lifespan Enhancement: Compared to traditional carbon steel or standard surface treatments, the structure's overall corrosion-resistant lifespan is increased by at least 3 times.
- Benefit: Significantly extends the structural life of the equipment, withstands extreme corrosive environments, and ensures long-term reliability of mechanical strength and electrical connections.
Comprehensive Benefits
- Precise Scenario Match: This solution is specifically designed to address the reliability pain points of AIS CTs in extremely harsh environments, including coastal substations, chemical park substations, salt-fog areas, and heavily polluted industrial zones.
- Significantly Enhanced Reliability: Through three key technological innovations (hydrophobic insulation, active anti-condensation, strong anti-corrosion), the equipment's MTBF (Mean Time Between Failures) can be elevated to over 250,000 hours (approx. 28.5 years).
- Safety and Economic Efficiency:
- Ensures Grid Security: Drastically reduces CT failure risks due to insulation flashover, condensation-induced shorts, and structural corrosion, preventing unplanned outages and major safety incidents.
- Extends Maintenance Intervals: Reduces frequent maintenance and replacement demands caused by environmental issues, significantly lowering Life-Cycle Cost (LCC).
- Improved Investment Return (ROI): One-time investment delivers long-term benefits, providing robust support for stable grid operation in extreme environments.
- Reduces Outage Losses: Avoids regional outages caused by CT failures, yielding substantial economic benefits – especially for critical industrial and civil consumers (e.g., preventing losses estimated at ¥0.5-1 million or higher for a typical 10-hour incident outage).
- Good accuracy & linearity performance: Flexible design, easy to meet requirements, relatively less affected by fast transients.